在科技不断发展的过程中,社会对于产品需求也逐渐朝着多样化的方向发展,从而要求的创新时间越来越短,品种及批量的比重也在不断的增加。PLC为可编程控制器,其可靠性较高,而且代码编写较为简单,还能够在线进行程序编写,及时找出编写过程中的问题和错误,以上优势使其性价比较高。
正是由于PLC此方面的性能,其被广泛应用到我国现社会生产活动中。将PLC技术应用在电气控制系统中,结合通信网络,可以优化及改进电气开关量,提高系统的柔性和可靠性,使电气控制系统的性能有进一步的优化及发展。
1系统的结构和组成
以PLC为基础的过程控制系统通过分布式控制结构实现,详见图1,下位机通过PLC设计,上位机通过计算机设计,通过RS-232C串口和PLC相互通信,以此实现工业现场工作的监控,从而实现工业现场的集中管理及分散控制,系统的网络结构图如图2所示。
图1 分布式控制结构图
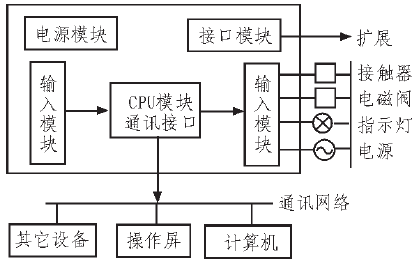
图2 系统的网络结构图
1.1网络
网络中的拓扑结构主要使用EtherNet网络,通过同轴电缆将生产监控相互连接,从而实现工业现场管理的集中化。
1.2监控
监控主要使用计算机作为上位机,通过组态王实现SCADA功能,使用RS串口和PLC相互通信,从而实现工业生产现场的监控。
1.3控制
使用C2541HD型号的PLC作为下位机,以此对工业生产现场进行控制,在PLC中设置电源模块、开关量输出模块/输入模块、模拟量输出模块/输入模块及RS串行接口。
模拟量输入模块的主要目的就是接受传感器发送的电流信号,并且将电流信号转换为BCD码数字量。通过拨号开关决定通道地址,本系统中的AD模块地址的开关为1,相应的IR区域为IR110-119。相应的DM区域为DM110-119.并且设置第一路转换器的工作不保持峰值,模拟量输入的通道地址表示为IR111,具体IR及DM地址的设置如表1所示。
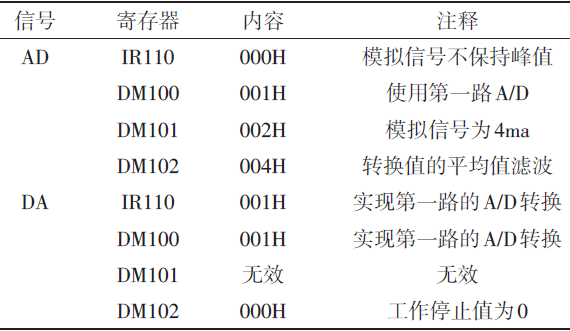
表1 IR 及DM 地址区域的设置
1.4控制通道
系统有两个控制通道,分别为输入及输出。输入通道使用投入式液位传感器,将现场的液位信号转换为电流信号,之后将其送至PLC模块中,传感部分使用高精度压力的传感器,实现压力信号到电信号的转换,从而实现和液面高度的正比,其精度、稳定性及可靠性都能够满足系统需求。
输出通道使用水泵及变频器组成,其能够接受PLC的输出控制量,使用变频器将电流变换为频率信号,实现水泵转速的改变,以此实现流量调节的作用。变频器使用交流变频器,使其能够对电动机转速进行控制。
2软件的设计和实现
软件主要包括监控软件、控制软件及下位机软件。
2.1监控软件
在现代工业控制过程中,计算机控制已经成为重要的部分,计算机控制系统的实施和设计都是创建系统的重要内容,其要和LPC创建以太网从而显示数据,还要显示数据。监控软件主要包括三套计算机,每个车间放置一台,操作人员对其进行操作,从而控制自身车间设备,还有一台放到经理办公室,从而实现生产车间的监控,便于对全厂生产情况的监控。监控软件中安装了组态软件、MOXA卡通讯软件、SQL数据库。通过组态软件能够连接PID仪表及PLC和计算机,实现数据的收集,通过良好的界面将整个工艺流程全面的展现出来,并且还能够对电机和阀门进行自动或者手动的开启及关闭,并且还有报警功能。允许工作人员对现场工况的快速查阅,故障记录的查阅,报表查询等。系统中的报警功能使工业生产过程不管是哪个部位出现故障,都会立刻报警,并且还具有报警闪烁。组态软件将生产过程中的数据及报表都存放到SQL数据库中,从而报表及查询。并且系统还开放OPC端口,能够将数据远程传送到管理员办公室,使管理人员能够实时的看到生产车间生产的情况。
2.2控制层
工厂主要包括多个公用设备车间及生产车间,从而能够对其有效控制,将PLC配置到每个生产车间中,在公用设备车间中配置远程I/O,控制层主要包括PLC及OID调节仪,通过PLC创建控制网,使CPU能够实现扩展,以此全面控制生产车间的设备情况。通过PLC中的开关量输出/输入、模拟量输出/输入等模块,能够实现阀门电机等多个设备的控制,检测温度、流量、压力及重量等,实现调节阀的控制及检测。控制程序使用模块化编程,有效提高了程序的可读性及简洁性。
为了能够实现数据的精准采集,使用脉冲计量仪表创建脉冲采集模块,使用此模块实现现场脉冲仪表数据的采集,之后对数据进行转换,以此对生产过程中设备进行控制。图3为工业生产中高速脉冲信号的过程,其主要作用就是将脉冲数量输送到缓存区。
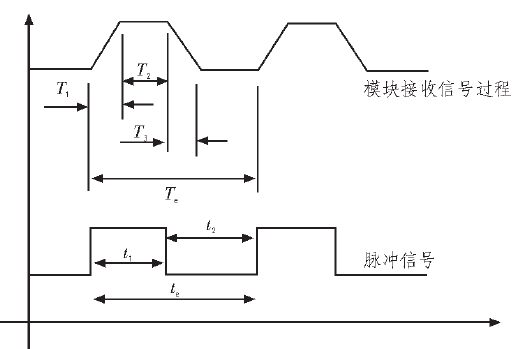
图3 工业生产中高速脉冲信号的过程
在PLC中以生产需求为基础,对自动程序进行编制,只要操作人员制定启动指令,就能够实现工业生产过程的流程。简单来说,也就是系统能够根据工艺需求,根据生产的顺序、工艺参数自动实现设备的生产。并且如果出现意外不能够生产,各个电机的设备都会自动变为手动,由操作人员对其进行开启及关闭。为了能够有效提高计算机和PLC通信的速度及安全性,本文使用以太网通信方式,在PLC中安装以太网模块,通过TCP/IP协议和计算机实现两者的通信,有效提高通信的流量及速度。控制层软件设计部分代码为:
publicDataSetgetDs(stringstrCon,string
tbname)
{
oledbcon=datacon.getCon();//获得数据库连接
oledbda=newOleDbDataAdapter(strCon,
oledbcon);//实例化OleDbDataAdapter对象
ds=newDataSet();//实例化DataSet对象
oledbda.Fill(ds,tbname);//填充DataSet数据集
returnds;
}
其主要目的是实现数据库设计。
2.3下位机
下位机软件设计是将监控及控制软件作为基础,通过OMRON编程软件实现下位机程序的编制及调试,之后将调制的程序在PLC中下载,下位机软件的主要目的就是实现PLC和监控软件两者的相互通信,控制现场水位及故障诊断,图4为主控制程序的过程。
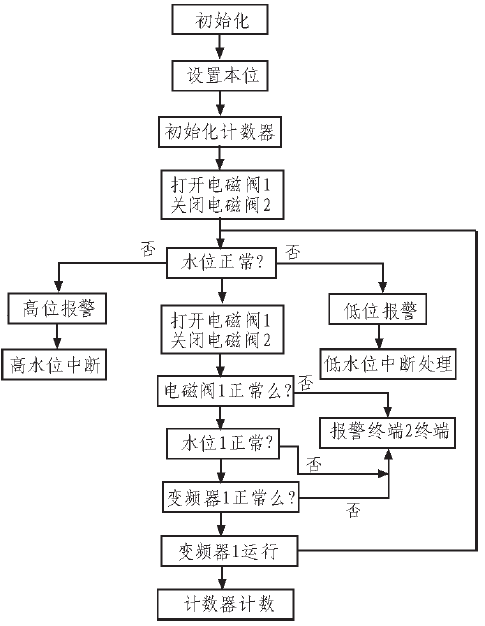
图4 主控制程序流程
系统初始化主要包括ROM、RAM及其他区域中的初始化和控制参数的设置。采样周期对检测参数、被控制对象及控制器有所影响,在实际使用过程中要充分考虑模拟量输入通道的数量及A/D的转换时间。因为系统采集的原始数据要根据实际情况处理,之后才能够被控制器使用,信号处理主要包括零点迁移、标度及量程变换等。在实际编程过程中,引入模糊控制能够提高控制系统的特点。模拟控制主要使用离线方式,通过输入语言变量附表和模糊控制原则创建控制规则查询表,之后实现系统的在线查询。
系统的故障诊断使用G2254型号PLC,其具有自动诊断功能,能够对现场控制系统的异常情况进行检测,比如指令的执行错误、PLC扫描周期的错误及端口通信错误等。
3结束语
文中将设计的系统投入使用,系统在运行过程中能够有效提高企业的工作效率,实现工作过程的全面监控。基于PLC的过程控制系统能够有效提高企业生产的自动化程度,降低生产过程中的人员,有效实现整个生产过程的控制,以此节约企业生产成本,提高企业生产质量及效率。